On the Norwegian shelf, there are currently 12 concrete facilities (Heidrun A and Troll B are floating), 64 fixed steel facilities and 20 floating steel facilities in operation. In addition, there are nearly 500 subsea installations. The concrete facilities account for about 70 per cent of the total weight of facilities on the shelf.
Field developments vary greatly with regard to size, complexity and number of facilities. Major fields can have development and operation in multiple phases, where some facilities are phased out while others are still operational. Larger and more comprehensive disposal projects must be carried out over several years. The Frigg field is, so far, the largest field on the shelf where decommissioning of the facilities has been completed. Production ceased in 2004, and the offshore disposal work started in 2005. The extensive disposal work on the field was completed in 2010.
The disposal process begins once a facility is no longer being used, and requires that the facility must be removed and the area cleared. The licensees are required to provide a detailed description of all phases of this process in a decommissioning plan. The plan must be submitted to the Ministry of Energy within two to five years prior to a licence expiring or being relinquished, or when use of a facility ceases.
The decommissioning plan consists of two main parts, a disposal part and an impact assessment part. The disposal part describes the technical and financial aspects of the cessation project. The impact assessment part provides an overview of expected consequences of the disposal, e.g., for the environment and other users of the sea. Both the proposed impact assessment programme and the actual impact assessment report must be submitted for public consultation.
Key principles for processing a decommissioning plan are that all financially profitable and recoverable oil and gas resources must have been produced, that the decommissioning project is cost-effective and that the project can be carried out within an acceptable framework regarding health, safety and environment (HSE) and other users of the sea. At present, the authorities have processed several decommissioning plans both for entire fields and for some facilities on fields in operation. Based on decommissioning plans, disposal decisions are made where final deadlines are set for the completion of removal projects.
A number of fields are now in a mature phase and have produced a large proportion of their original reserves. At the same time, the fields that are expected to be shut down in the near future have little impact on the total production on the shelf. However, it is difficult to estimate exactly when producing fields will shut down. Usually, facilities stay on fields longer than planned for in the development stage. On many fields, new tie-ins (satellite fields) and improved recovery initiatives have extended field lifetimes beyond what was estimated in the plan for development and operation (PDO). The commercial life of facilities which are no longer producing from their own deposits may be extended if they can function as host installations for other developments in the area. It is therefore important to explore all opportunities for utilising such facilities before a final disposal decision.
Cessation of the petroleum activities and disposal of facilities are regulated by the Petroleum Act and Petroleum Regulations. Norway acts also in accordance with international regulations and agreements, such as the Oslo-Paris Convention (OSPAR), which stipulates that petroleum facilities can be abandoned after shutdown only in highly extraordinary scenarios.
Section 5-3 of the Petroleum Act stipulates that the Ministry of Energy makes disposal decisions. Article 60 of the United Nations Convention on the Law of the Sea (UNCLOS) stipulates that facilities shall, as a rule, be removed, and that both removal and potential abandonment shall take place in accordance with internationally accepted standards. In accordance with this and the OSPAR Convention, the authorities decide on removal of subsea facilities, floating steel facilities and the topsides of concrete installations. However, if disposal of concrete facilities and the jacket on large, fixed steel facilities is subject to OSPAR consultation, it is assumed that countries considering offshore disposal must consult the other countries that are parties to the OSPAR Convention before national authorities take disposal measures.
The Ministry has so far processed more than 20 disposal plans. Two permits have been granted to leave parts of an offshore installation under the exemption provision of OSPAR decision 98/3. This applies to the concrete substructure of the Ekofisk tank and concrete substructure on the Frigg field. Such permissions was granted following consultation in accordance with the OSPAR Convention.
Pipelines are not covered by the OSPAR Convention. The choice of disposal options is determined in each individual case based on a comprehensive evaluation, where costs are assessed in relation to the consequences for safety, environment, fisheries and other users of the sea.
See this information from Norwegian Offshore Directorate for more details (in Norwegian).
Facilities that are not re-used or abandoned on the field must be transported to land and handled at a permitted facility for scrapping and recycling or disposal. Most of the waste from the petroleum activities (98 per cent) is recyclable steel. However, there will also be waste that requires special handling. The facilities that have a permit under the Pollution Control Act to demolish offshore installations are to be find on Norwegian Environment Agency’s website.
Since the scrapping facilities in Norway are located on deep fjords and have deep-water quays, other countries on the North Sea are likely to consider utilising these facilities in the future.
AF Miljøbase Vats – Installations landed from the Ekofisk area
Photo: Ellen Marie Hagevik, Medvind24
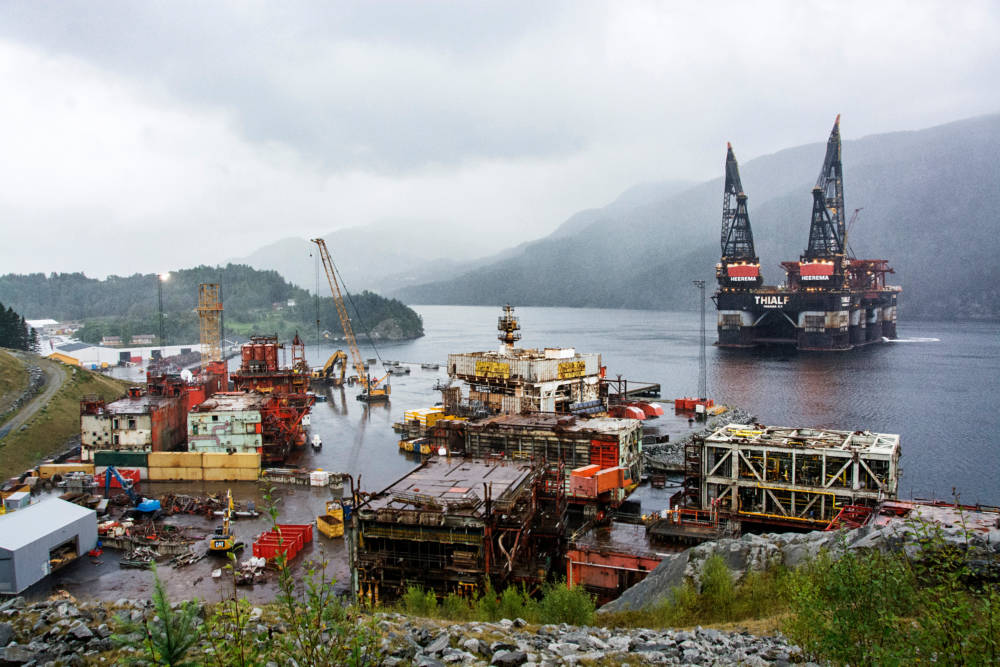
The costs related to shutdown and disposal of facilities are relatively small compared to the costs related to exploration, development and operations and the revenue from the field. Costs related to decommissioning are uncertain and vary from field to field. The largest cost elements in disposal projects are related to permanent plugging of wells and removal of the offshore facilities.
Cooperation between licensees, the service and supply industry, the authorities and affected interest groups is crucial for cost-effective disposal activities in the future, and in turn contributes to reducing costs.